精密加工の世界では、技術の進歩に伴い様々な加工法が発展してきました。その中でも、エッチング加工は独自の特徴を持ち、多くの産業分野で重要な役割を果たしています。
本記事では、エッチング加工の特徴を他の加工法と比較しながら、自社に最適な加工法を選ぶためのガイドラインを提供します。
エッチング加工の概要
エッチング加工とは、化学薬品を使用して金属や他の材料を溶かし、目的の形状や模様を作り出す加工技術です。この方法は、特に薄い金属板や箔の精密加工に適しており、電子部品、半導体、医療機器、航空宇宙産業など、高度な精度が要求される分野で広く利用されています。
エッチング加工が選ばれる主な理由は、以下の通りです。
1. 高精度な加工が可能
2. 複雑な形状やパターンの作成に適する
3. 材料にストレスを与えない非接触加工が可能
4. 薄い材料でも変形せずに加工が可能
例えば、スマートフォンの内部に使用される微細な電子部品や、医療用インプラントの精密部品など、ミクロンレベルの精度が要求される製品の製造にエッチング加工が活用されています。
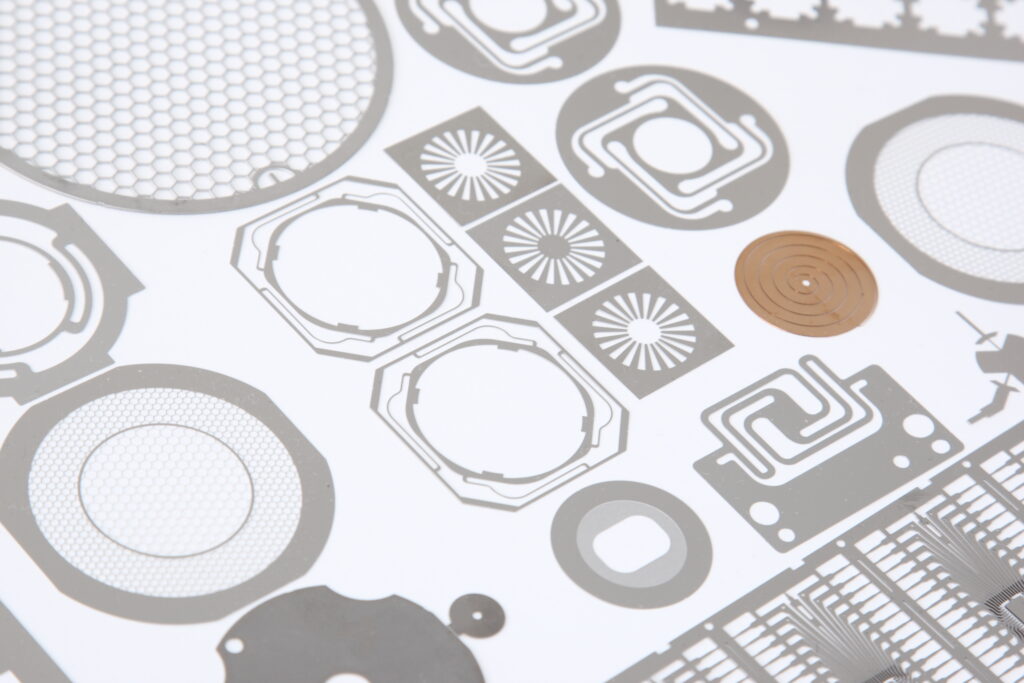
エッチング加工と他加工法の比較表
特性 | エッチング加工 | 微細レーザー加工 | 機械加工 | プレス加工 |
---|---|---|---|---|
精度 | 高 ±0.01mm | 中~高 ±0.05mm~0.01mm | 中~高 ±0.05mm~0.01mm | 中 ±0.05mm |
主な材料 | 金属板・箔 | 金属、木材、 プラスチック | 金属、木材、 プラスチック | 金属 |
材料の厚さ | 極薄~薄 0.004mm~2mm程度 | 薄~中 ~10mm | 制限なし | 中 0.1mm~10mm |
初期コスト | 低 フォトマスクのみ | 低 | 低 | 高 金型製作が必要 |
得意範囲 | 小~中ロットで高 (1個~数万) | 小ロットで高 | 小~中ロットで中 | 大ロットで高 |
材料への負荷 | 低 | 熱影響あり | 高 | 高 |
微細加工 | ◎ 0.05mm~ | 〇 0.02mm程度~ | △ 工具サイズに制限あり | × 微細加工は困難 |
設計の自由度 | 高 拡散接合との組み合わせにより3D可 | 高 | 高 | 低 金型の制約あり |
主な用途 | 電子部品、シム、 精密フィルター | 切断、マーキング、 微細穴あけ | 機械部品、 金型、試作品 | 自動車部品、家電部品、 金属加工品 |
エッチング加工、微細レーザー加工、機械加工、プレス加工の4つの主要な加工法について、その特性を比較した表です。
この表を参考に、各加工法との比較を詳しく見ていきましょう。
各加工法の比較
1.微細レーザー加工との比較
エッチング加工と微細レーザー加工は、どちらも高精度な加工が可能ですが、それぞれに特徴があります。
ー精度
エッチング加工は±0.01mm程度の高精度加工が可能で、特に薄い材料の加工に優れています。一方、微細レーザー加工は±0.05mm~0.01mm程度の精度を持ち、より厚い材料にも対応できます。
ー材料
エッチング加工は主に金属材料に適していますが、微細レーザー加工は金属以外にもプラスチックや木材など、幅広い材料に対応可能です。
ー加工速度
エッチング加工はバッチ処理による同時加工が可能ですが、微細レーザー加工は1点ずつの加工となるので時間がかかります。ただし、微細レーザー加工は1点ずつであれば複雑な形状の加工が速いという特徴があります。
2.機械加工との比較
エッチング加工と機械加工(切削加工やフライス加工など)は、それぞれ異なる特性を持っています。
ー複雑なデザイン
エッチング加工は複雑な2Dパターンを一度に加工可能で、拡散接合との組み合わせにより3D形状の加工も可能です。機械加工は複雑な3D形状の加工が可能ですが、微細なパターンの加工には制限があります。
ー非接触加工
エッチング加工は化学的に材料を溶かすため、材料にストレスを与えません。一方、機械加工は工具が直接材料に接触するため、特に薄い材料では変形のリスクがあります。
ー材料の制限
エッチング加工は主に金属材料に限定されますが、機械加工は金属、プラスチック、木材など幅広い材料に対応可能です。
3.プレス加工との比較
エッチング加工とプレス加工は、金属加工の分野で広く使用されていますが、それぞれに長所と短所があります。
ー効率性
エッチング加工は中小ロットの生産に適していますが、プレス加工は高速で連続的な加工が可能で、大量生産に非常に適しています。
ー形状の自由
エッチング加工は複雑な形状や微細なパターンの加工が可能です。プレス加工は薄い金属の加工に適しておらず、また金型の制約により比較的単純な形状に限定されます。
ー初期コスト
エッチング加工は初期設備投資が比較的低いですが、プレス加工は金型製作に高いコストがかかります。
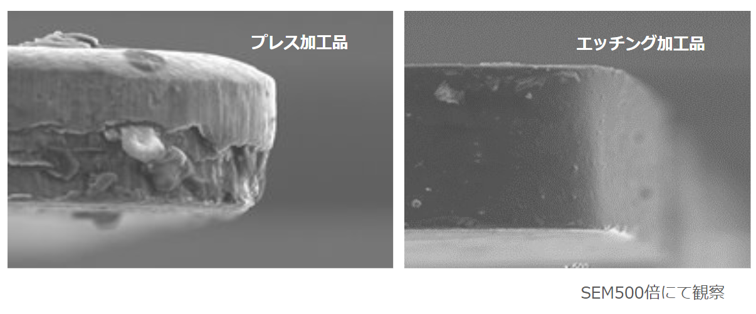
エッチング加工の活用事例
シム・スペーサーの製造
シム・スペーサーは、機械部品間の微細な隙間を調整するために使用される極薄の金属板です。フォトエッチング加工は、この精密部品の製造に最適です。
- 高精度:厚さ方向の精度が±0.005mm程度
- 均一性:化学的プロセスにより、全体で均一な厚さを実現
- 複雑形状:円形や異形のシム・スペーサーも容易に製造可能
エッチング加工 vs プレス加工
エッチング加工:
最薄0.004mmの極薄材料でも精密に加工可能。小ロット生産に適する
プレス加工:
極薄材料の加工は困難。金型製作のコストが高く、大量生産向き
応用例:
航空機エンジンの部品調整
精密機械の組立
光学機器の位置調整
コールドプレートの微細流路製造
エッチング加工は、拡散接合との組み合わせによりコールドプレートなどの熱管理デバイスに必要な微細流路の製造に非常に適しています。
- 高精度:±0.01mmの精度で流路を形成可能
- 複雑なパターン:蛇行や分岐を含む複雑な流路設計に対応 均一な深さ:化学的なプロセスにより、流路の深さを均一に保つことが可能。
エッチング加工 vs 機械加工
エッチング加工:
0.1mm以下の微細な流路も加工可能。材料にストレスを与えないため、薄い金属板でも変形しにくい。
機械加工:
微細な流路の加工は困難。工具の摩耗や振動により、精度の維持が難しい。
応用例:
半導体製造装置の冷却システム
高出力LEDの熱管理
医療機器の温度制御
高精度フィルタの製造
エッチング加工は、微細な穴や複雑なパターンを持つ高精度フィルタの製造に適しています。
- 微細加工:直径0.05mm~の穴加工が可能
- 均一性:全ての穴のサイズと形状が均一
- 複雑パターン:特殊な流体制御のための複雑なパターンも実現可能
エッチング加工 vs 微細レーザー加工
エッチング加工:
熱影響がないため、穴の周囲にバリや変形が生じにくい。多数の穴を同時に加工できる。
微細レーザー加工:
熱影響により、微細な穴の周囲に変形が生じやすい。穴を1つずつ加工するため、時間とコストがかかる。
応用例:
医療用輸液フィルタ
燃料噴射ノズル
精密な気体・液体フィルタリングシステム
まとめ
エッチング加工は、高精度、複雑形状、非接触加工という特性を活かし、様々な産業分野で重要な役割を果たしています。特に、微細加工や薄材加工が必要な場面では、他の加工法に比べて優位性を発揮します。自社の製品や要求仕様に応じて、エッチング加工と他の加工法を適切に選択することで、品質向上とコスト削減を同時に実現できる可能性があります。製品の特性、生産量、要求精度などを総合的に考慮し、最適な加工法を選択することが重要です。