プローブピンとは
プローブピンは、電気的な検査において被測定物に接触して電気信号を伝達する重要な部品です。検査工程における信頼性の要となるため、その特性と適切な使用方法の理解は非常に重要です。
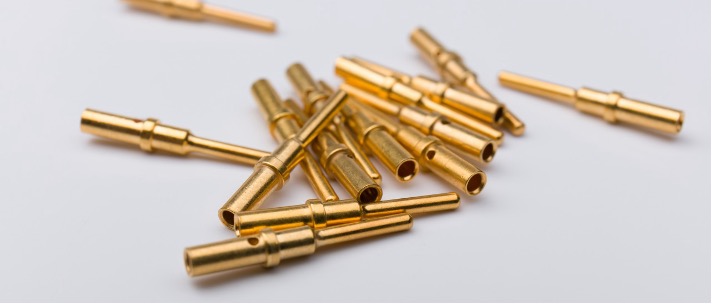
プローブピンの主な特徴として、以下が挙げられます。
優れた導電性
金やベリリウム銅などの高導電性材料を使用し、正確な信号伝達を実現します。これにより、微小な電気信号も確実に検出することが可能となり、高精度な検査を実現できます。
安定した接触力
ばね構造により一定の接触圧を維持します。この特性により、被測定物への均一な接触が保証され、測定の再現性が向上します。また、被測定物の表面状態の変化に対しても安定した接触を確保できます。
高い耐久性
繰り返しの使用に耐える設計となっています。特に、摩耗や疲労に対する考慮がなされており、長期間の使用でも性能を維持できます。
プローブピンの使用例
使用例としては、以下のような幅広い応用があります。
- 半導体のウェハテスト:ウェハ上の各ダイの電気特性を検査
- ICパッケージの最終検査:組立後の製品の機能確認
- プリント基板の導通試験:配線パターンの導通確認
- 電子部品の特性評価:抵抗やコンデンサなどの部品検査
- 自動車電装品の検査:各種センサーやECUの動作確認
これらの検査工程では、プローブピンの性能が直接的に検査精度と生産性に影響を与えるため、適切な選定と管理が不可欠です。
プローブピンの技術的課題と解決策
接触不良への対応
接触不良は検査の信頼性を直接左右する重要な問題です。主な原因として、被測定物表面の酸化膜や異物の付着、接触圧力の不足などが挙げられます。この問題は、特に微細な端子や高速動作する製品の検査において深刻な影響を及ぼします。
解決策として、以下のアプローチが効果的です。
– 適切な接触圧力の設定
被測定物の特性に応じて最適な接触圧力を設定することで、安定した接触を確保します。過度な圧力は被測定物を損傷させる可能性があり、逆に不足すると接触不良の原因となります。
– 先端形状の最適化
セレーション加工などの表面処理により、酸化膜を破壊し、確実な電気的接触を実現します。被測定物の材質や表面状態に応じて、最適な加工方法を選択することが重要です。
– 定期的なクリーニング手順の確立
異物や酸化物の蓄積を防ぐため、適切なクリーニング間隔と方法を設定します。超音波洗浄や専用クリーナーの使用など、効果的な清掃方法の採用が推奨されます。
– 接触部の表面処理
金メッキなどの表面処理により、耐酸化性と導電性を向上させます。メッキ厚さや材質の選択は、使用環境と要求される耐久性を考慮して決定します。
プローブピンの摩耗・寿命対策
繰り返しの使用による摩耗は避けられない問題ですが、適切な対策により寿命を大幅に延ばすことが可能です。特に、高速検査や大量生産ラインでは、プローブピンの寿命が生産性に直接影響を与えます。
対策ポイントとして、以下の要素を考慮する必要があります。
– 使用環境に適した材質選択
温度条件や接触回数などの使用条件に基づいて、最適な材質を選定します。例えば、高温環境では耐熱性の高い材質を、高頻度使用では耐摩耗性の優れた材質を選択します。
– 定期的な点検と交換基準の設定
摩耗状態を定量的に評価し、適切なタイミングでの交換を実施します。点検項目には、外観検査、導通試験、接触抵抗測定などが含まれます。
– 適切な接触圧力の管理
過度な接触圧力は摩耗を加速させるため、必要最小限の圧力で安定した接触が得られるよう調整します。圧力管理には、専用の計測器を用いた定期的な確認が推奨されます。
– 摩耗に強い表面処理の採用
硬質クロムメッキや窒化処理など、耐摩耗性を向上させる表面処理を施すことで、寿命を延長できます。
測定精度の向上
高精度な測定を実現するためには、以下の要素を総合的に考慮する必要があります。
– 接触抵抗の安定化
接触面積の確保と表面処理の最適化により、接触抵抗のばらつきを最小限に抑えます。特に、微小信号の測定では、接触抵抗の変動が測定結果に大きく影響を与えるため、慎重な管理が必要です。
– ノイズの低減
シールド構造の採用や配線経路の最適化により、外部ノイズの影響を低減します。高感度な測定では、接地方法やケーブル配置にも注意を払う必要があります。
– 温度変化の影響への対策
測定環境の温度管理や、温度補償機能の導入により、温度変化による測定誤差を抑制します。特に、長時間の連続測定では、温度ドリフトの影響を考慮する必要があります。
– 機械的な位置決め精度の確保
プローブピンの取り付け精度や、被測定物との位置合わせ精度を向上させることで、安定した接触を実現します。
高周波・大電流測定時の課題
高周波測定時には信号の減衰やクロストークが、大電流測定時には発熱や電圧降下が問題となります。これらの課題に対しては、以下のような対策が有効です。
– インピーダンス整合の最適化
伝送線路の特性インピーダンスを考慮した設計により、信号の反射や減衰を抑制します。プローブピンの構造や配置にも注意を払い、高周波特性を維持します。
– シールド構造の採用
適切なシールド設計により、クロストークやノイズの影響を最小限に抑えます。シールドの接地方法や、隣接ピン間の遮蔽なども重要な要素となります。
– 放熱設計の改善
大電流測定時の発熱対策として、効果的な放熱構造を採用します。冷却機構の導入や、熱伝導性の高い材料の使用なども検討します。
– 断面積の適正化
電流密度を考慮した導体断面積の設計により、発熱や電圧降下を抑制します。ただし、機械的強度との両立が必要です。
プローブピン選定のポイント
種類の選択
用途に応じて適切な種類を選択することが重要です。主な種類と特徴は以下の通りです。
– スプリング方式
- 一般的な用途に適し、コストパフォーマンスに優れます
- ストロークが大きく、位置ずれに対する許容度が高い
- メンテナンス性が良好で、部品交換が容易
- 様々なバネ特性が選択可能
– カンチレバー方式
- 微小ピッチに対応可能
- 横方向からのアプローチが可能
- 接触圧力の調整が容易
- スクラビング効果により接触安定性が向上
– バーチカル方式
- 高周波測定に適する
- インピーダンス整合が容易
- 小型化が可能
- 機械的安定性が高い
先端形状の最適化
被測定物の特性に合わせた先端形状の選択が必要です。各形状の特徴と適用例は以下の通りです。
– 円錐型
- 標準的な用途に適する
- 接触点が安定
- 様々な被測定物に対応可能
- 製造コストが比較的低い
– クラウン型
- 酸化膜の除去効果が高い
- 多点接触により安定性が向上
- スクラビング効果が大きい
- 被測定物への損傷に注意が必要
– 平面型
- パッド損傷を抑制
- 接触面積が大きく、低接触抵抗
- 大電流測定に適する
- 位置ずれに対する許容度が小さい
– ニードル型
- 微細端子への対応が可能
- 高密度実装に適する
- 接触圧力が集中しやすい
- 先端の摩耗に注意が必要
材質選択のポイント
要求特性に応じて適切な材質を選択します。主な材質の特徴は以下の通りです。
– リン青銅
- 標準的な用途に適する
- コストパフォーマンスが良好
- 機械的特性がバランス良好
- 加工性に優れる
– ベリリウム銅
- 高強度・高導電性が必要な場合に最適
- 耐疲労性に優れる
- 高温特性が良好
- 価格が比較的高い
– タングステン
- 耐摩耗性に優れる
- 高硬度
- 熱膨張係数が小さい
- 加工性に制限あり
– 貴金属合金
- 高信頼性要求時に使用
- 耐食性に優れる
- 低接触抵抗
- コストが高い