Test Socket for Miniaturized and Narrow-pitch Semiconductor IC Test
What is MMS (Micro Metal Socket®)?
A test socket is an essential component used to evaluate the high performance semiconductor devices, functioning as the interface between the device and the test equipment. It is a crucial part that influences the accuracy and reliability of tests.
MMS is an innovative test socket designed to meet the demands of evolving semiconductor technology. As the need for high-frequency and high-current compatibility increases, semiconductor test needs high performance. Additionally, sockets that can accommodate the miniaturization of semiconductors and narrower terminal pitches are required. MMS addresses these needs, contributing to the development and production of next-generation semiconductors.
Micro Metal Socket®
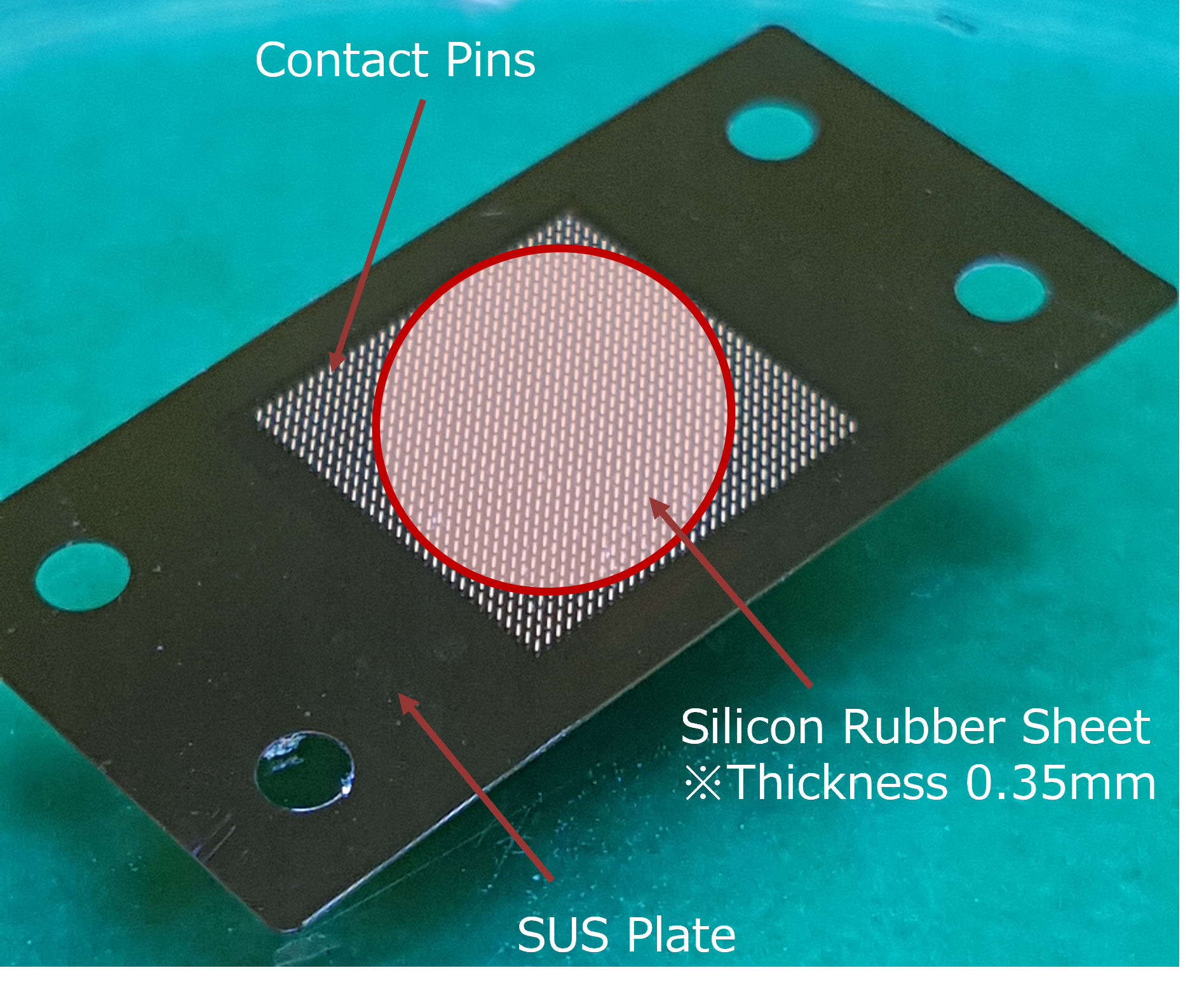
The holes for socket mounting can be freely arranged.
Key Feature
- Min Contact height: 0.45mm
- Min Contact pitch: 0.15mm
- High-frequency transmission characteristics with ultra-short transmission paths (60GHz @ -1dB)
- Force / displacement: 0.10N / 0.1mm
Performance
- Support high-speed/frequency transmission at 60GHz @ -1dB
- Rated current: 1A per contact (with a contact height of 0.45mm)
Note: We offer the optimal product based on the dimensions, terminal pitch, and load requirements of the device under test.
Advantages of MMS
1.Unique Materials for High-Frequency and High-Current Applications
MMS achieves high-frequency transmission through ultra-short paths by developing micro contacts with a minimum contact height of 0.45mm. Even at 0.45mm contact height, MMS supports a rated current of 1A, eliminating the issues caused by contact resistance in semiconductor package test and enabling more stable test processes.
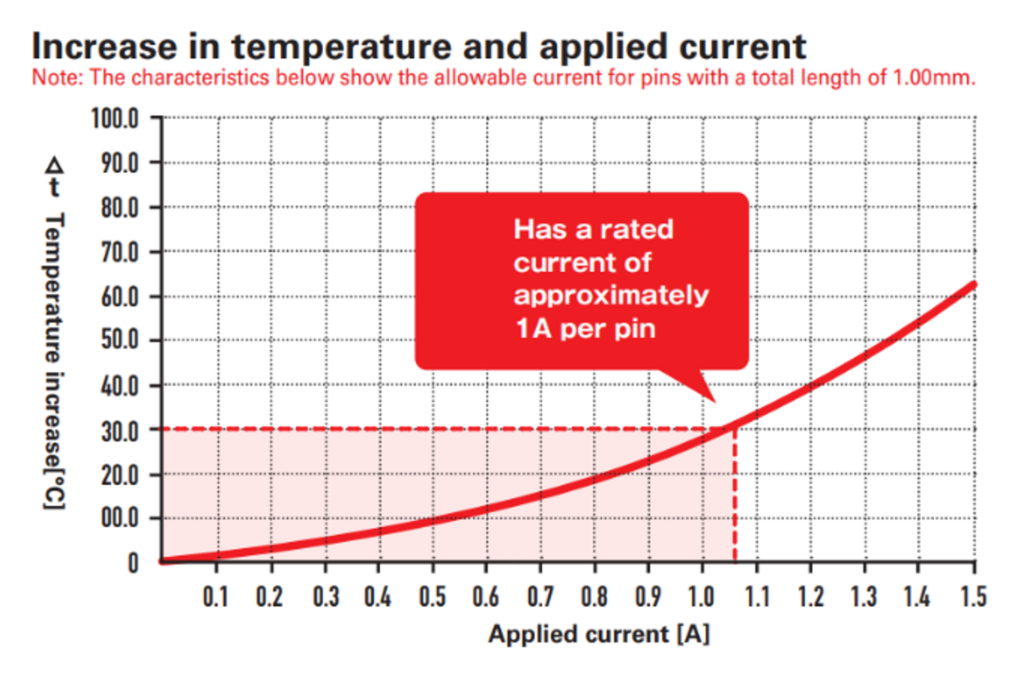
2.Proprietary Contact Structure for Low Force Load and Reliable Contact
MMS uses a single-piece contact structure. Without internal contact structures, MMS achieves a low load of 0.10N per contact, reducing the stress on test handlers by approximately 80% compared with conventional sockets. Additionally, as a sheet-type contact for high-frequency measurement, MMS reaches both electrical and mechanical lifespans of 50,000 touchdowns.
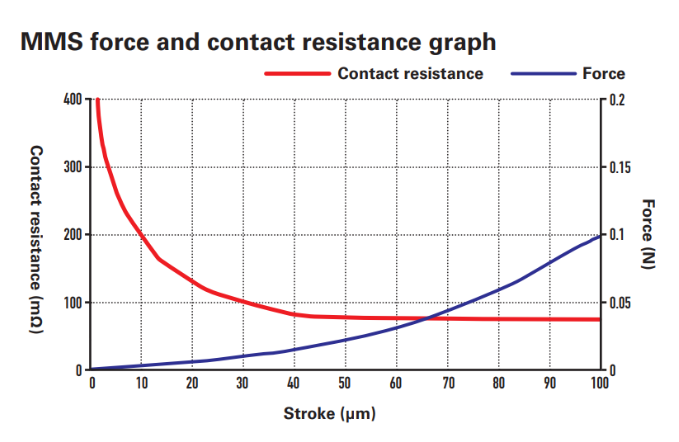
3.Industry-Leading Minimum Contact Pitch
MMS supports miniaturization, multi-pin, and narrow-pitch applications, with a pitch as small as 0.15mm, ideal for next-generation semiconductor test. The housing-free structure allows for customizable sheets tailored to specific applications and requirements, supporting both smartphone packages and future semiconductor technologies requiring narrow-pitch solutions.
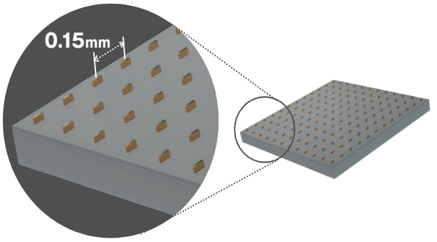
Examples of MMS Applications
Narrow Pitch IC Packages
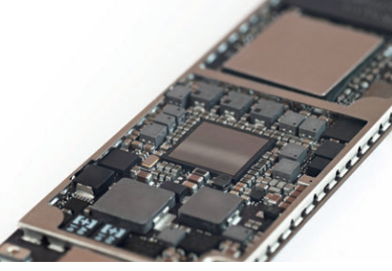
As semiconductor technology advances, IC packages become more compact, high-performance, and highly integrated, leading to narrower pitches. MMS, with a minimum pitch of 0.15mm, is the perfect solution for test next-generation and even further advanced IC packages.
High-Pin-Count BGA Packages
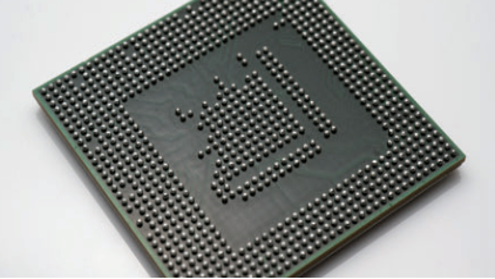
The pin counts of BGA package is increasing, and more low force is required at final test phase. MMS supports low force of 0.10N per pin (1/5 of conventional sockets), extends the lifespan of test equipment.
Interposer
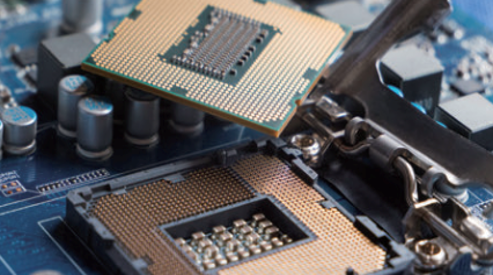
MMS is also ideal for use as an interposer, offering pin layouts customized for specific IC package and board designs.
Camera Modules
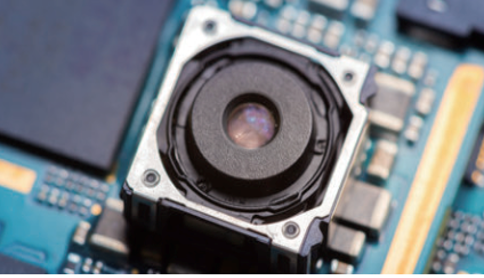
MMS is suitable solution for test of high-resolution camera module as well, because MMS supports stable connection with high-frequency.
Communication Modules
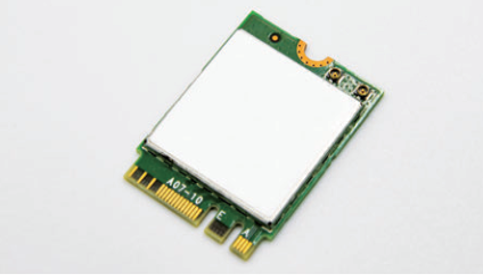
MMS provides with stable high-frequency connectivity, making it a reliable choice for test communication modules.
Use-Cases of MMS
Use Case 1: Semiconductor IC Final Test
Customer’s Challenge
It is difficult to measure to high-frequency (millimeter-wave) signal stably by pogo-pins or rubber sockets.
UPT’s Solution
MMS is one piece structure and supports stable high-frequency characteristics. UPT solves this issue by customizing the design.
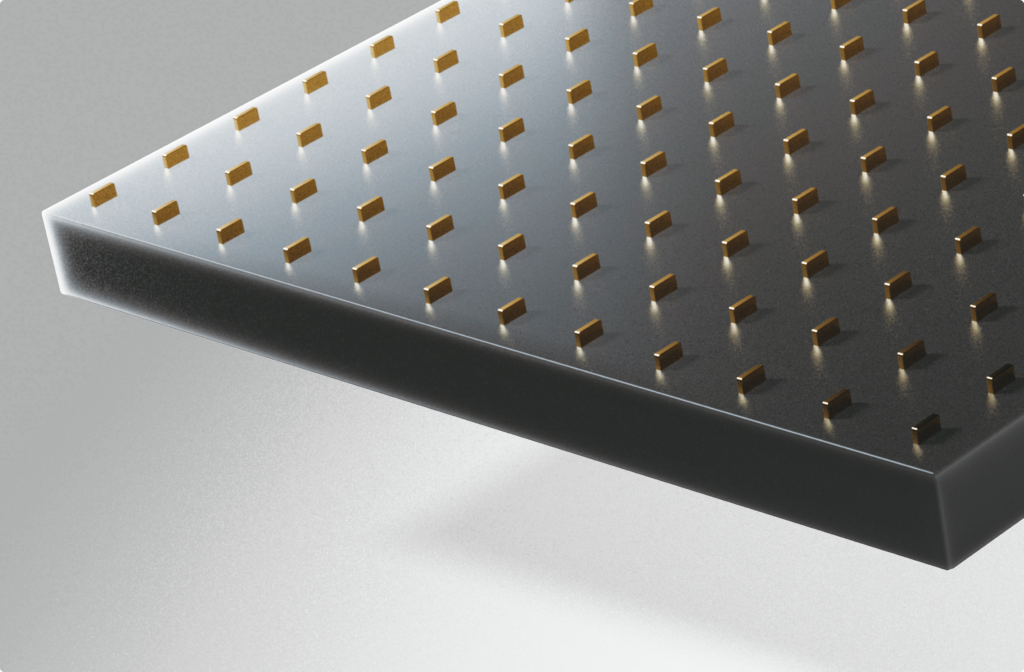
Use Case 2: BGA Ball Guide
Customer’s Challenge:
As the pitch of BGA solder balls narrowed in semiconductor IC final test, existing methods that positioned the BGA solder balls and test probe pins using the BGA package outline frequently caused misalignment.
UPT’s Solution:
Using a BGA ball guide in conjunction with MMS ensured precise positioning of BGA solder balls and test probe pins, preventing misalignment and ensuring stable contact.
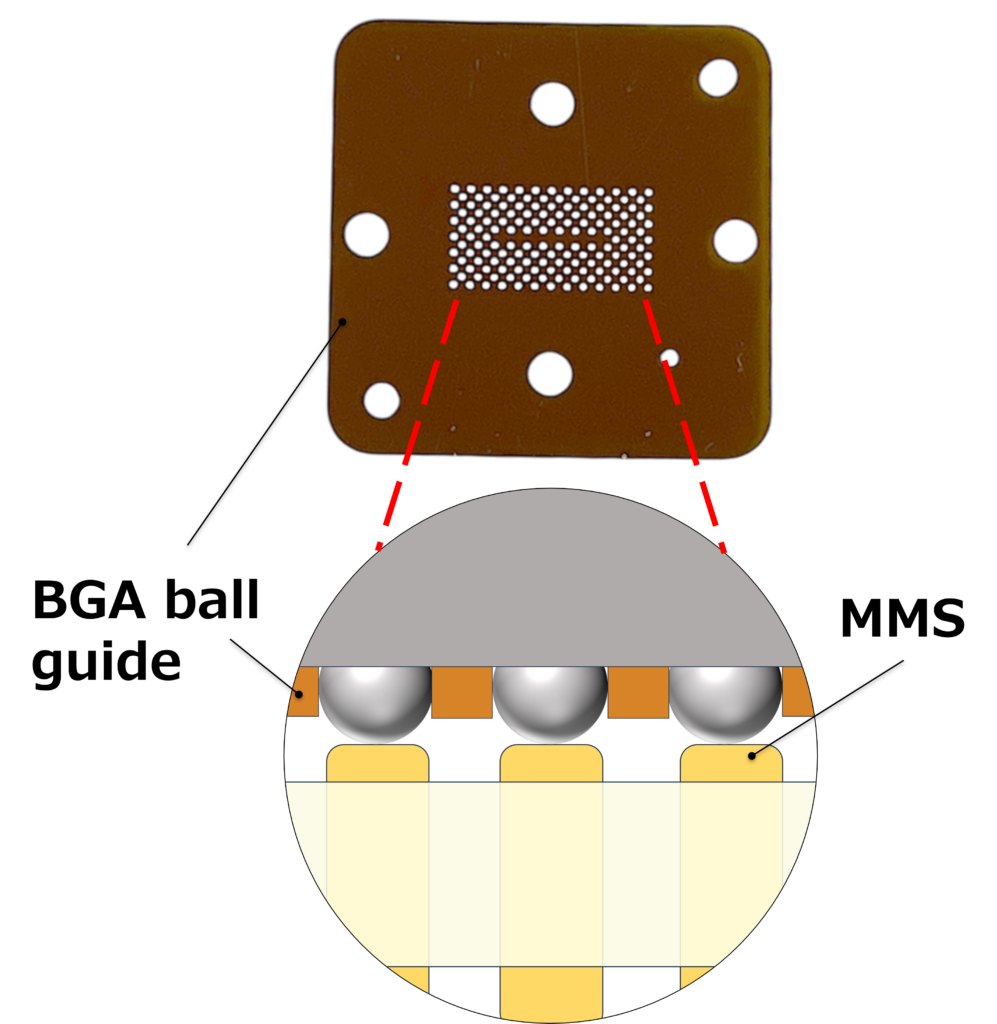