Electronic Component Trays with Photo Etching + Diffusion Bonding Technology | Supports Complex Shapes and Precision Machining
What are Electronic Component Trays?
Electronic component trays specialize for transporting electronic components and semiconductors. They secure components with high-precision shapes to prevent damage, reduce product loss, and improve yield rates.
Electronic component trays are typically designed with anti-static measures to prevent damage from static electricity and are made from materials with excellent heat resistance and durability. The design also enables efficient transportation, taking into account compatibility with automated transport systems in factories. This helps maintain the quality of electronic components and semiconductors while improving production efficiency.
Magnetic materials can also be selected, making it easy to attach components to metal housings. These trays offer high durability, making their life time longer. They can also be used as transport carriers in processes such as cleaning fixed components and sputtering.
UPT combines photo etching with diffusion bonding technology to manufacture transport trays tailored to customer applications, supporting complex shapes and precision machining. If you’re looking for high-precision, high-strength transport trays, feel free to contact us.
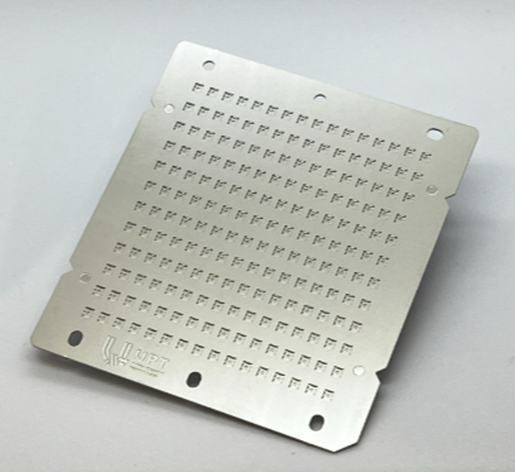
Example of Manufacturing: Electronic Component Tray
We layer multiple metal sheets processed with photo etching technology and join them at an atomic level with diffusion bonding technology. This method allows to create ideal cavities, and enables stable and precise positioning of ultra-small electronic components, significantly improving production efficiency in tasks like part insertion and retrieval.
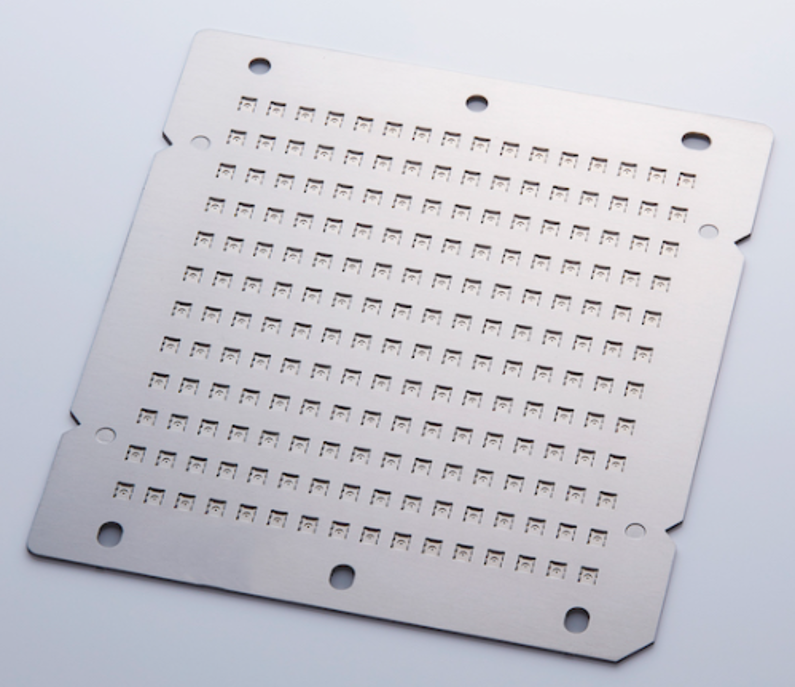
Material: SUS304
Thickness: t0.8mm (4 layers of t0.2mm each)
Outer dimensions: 80mm × 90mm
Number of cavities: 12 × 16 (192 cavities)
Hole Dimensions
1st layer: 2.1mm × 2.5mm
2nd layer: 1.7mm × 2.1mm
3rd layer: Φ0.15mm
4th layer: Φ0.25mm
Differences from Other Methods
Here are differences between our manufacturing method (photo etching + diffusion bonding technology), and other methods.
VS Machined Products
In terms of quality, machinig has limits to creating complex shapes, and the design flexibility is not the best. This makes it difficult to produce trays with ideal shapes, especially when processing narrow-pitch designs. In terms of cost, machining also requires deburring, which increases expenses, and producing trays with many cavities becomes even more costly as each cavity must be individually processed. Additionally, it is challenging to achieve cost efficiency through mass production.
VS Welded Products
In terms of precision, the heating and melting process in welding often causes material changes and deformations, making it difficult to maintain dimensional accuracy. Therefore, welding is not suitable for producing parts that require high precision. Regarding strength, welding joins only the periphery of the object, whereas diffusion bonding uniformly joins the entire surface, resulting in stronger joints compared with welded parts.