Improve heat dissipation performance and design freedom with photo-etching & diffusion bonding technologies
A backing plate acts as both a discharge electrode and a cooling plate. UPT combines “photo-eching” and “diffusion bonding” technologies to provide products with high-performance microchannel structures. Should you have any issues with heat dissipation performance or design flexibility, please feel free to contact us.
What is a backing plate?
Metal thin films for semiconductors and LCD panels are produced by a method called sputtering. Sputtering is a film formation method in which inert gas ions such as argon ionized by plasma collid with a target metal and ejected atoms deposit.
As the target metal becomes hot, sputtering proceeds with cooling, which requires a backing plate.
The main roles of the backing plate are
1. as an electrode for electrical discharge
2. as a cooling plate to prevent the target metal from being too hot
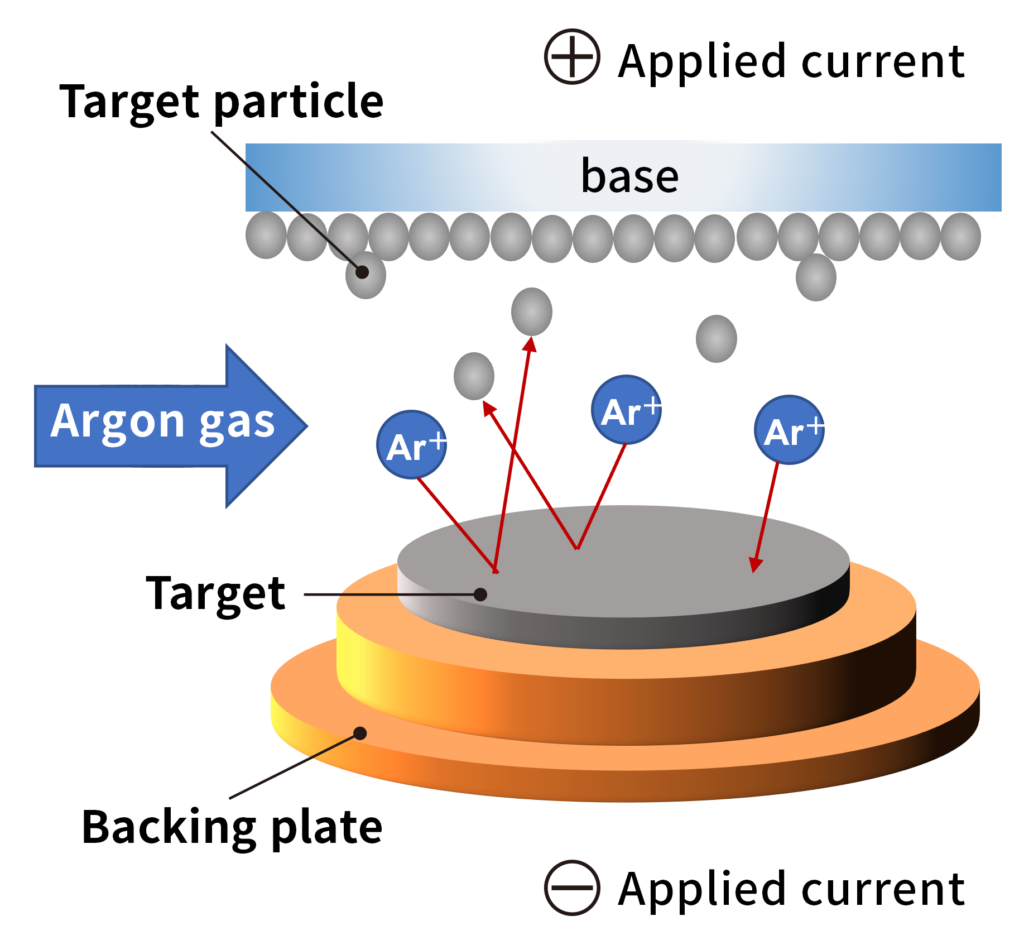
UPT’s Core Technologies
UPT manufactures backing plates with high-performance microfluidic structures by combining its core technologies of “photo-etching” and “diffusion bonding”. Photo-etching uses an etching solution to chemically react and corrode metal, enabling precision processing of thin sheet metal. It creates complex flow channel structures and improves the heat dissipation of the backing plate. Diffusion bonding, on the other hand, joins metal surfaces together at the atomic level to produce a metal part with a 3D internal structure. This technology creates a bonding surface with no gaps, achieving an ideal heat dissipation effect. The combination of these technologies can create a backing plate with high heat dissipation performance even in a small (thin) package.
- Combination of photo-etching and diffusion bonding can create complex flow paths and hollow structures that cannot be achieved by cutting or other methods
- Diffusion bonding does not use brazing or adhesives, so the structure is resistant to deformation and deterioration
- Diffusion bonding at the level of inter-elemental bonding allows for an ideal heat dissipation by eliminating the gaps at the bonding surface
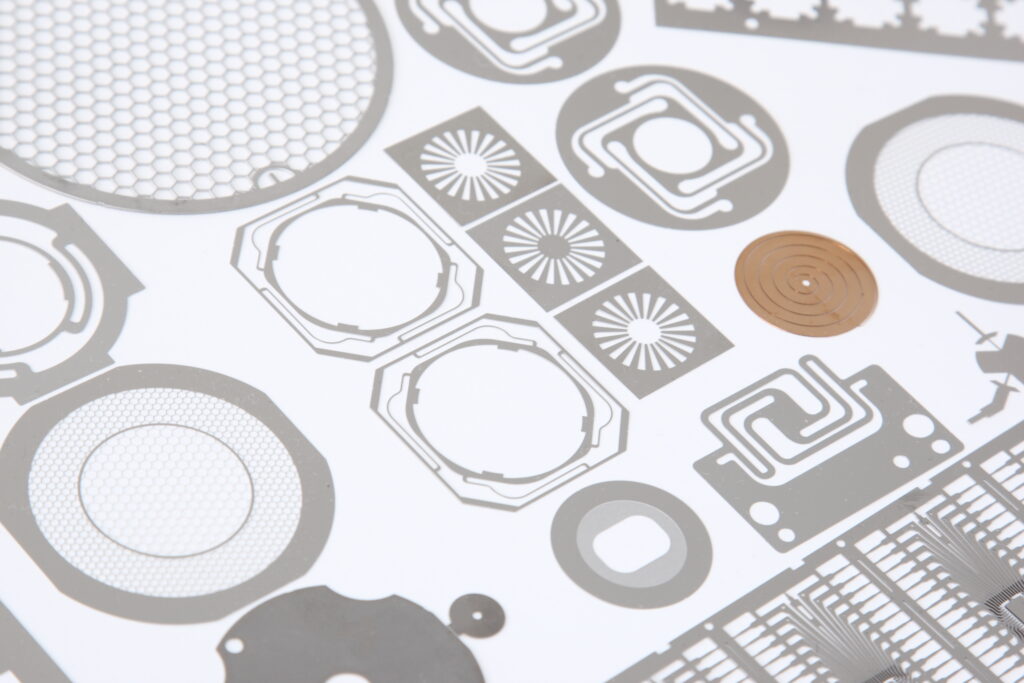
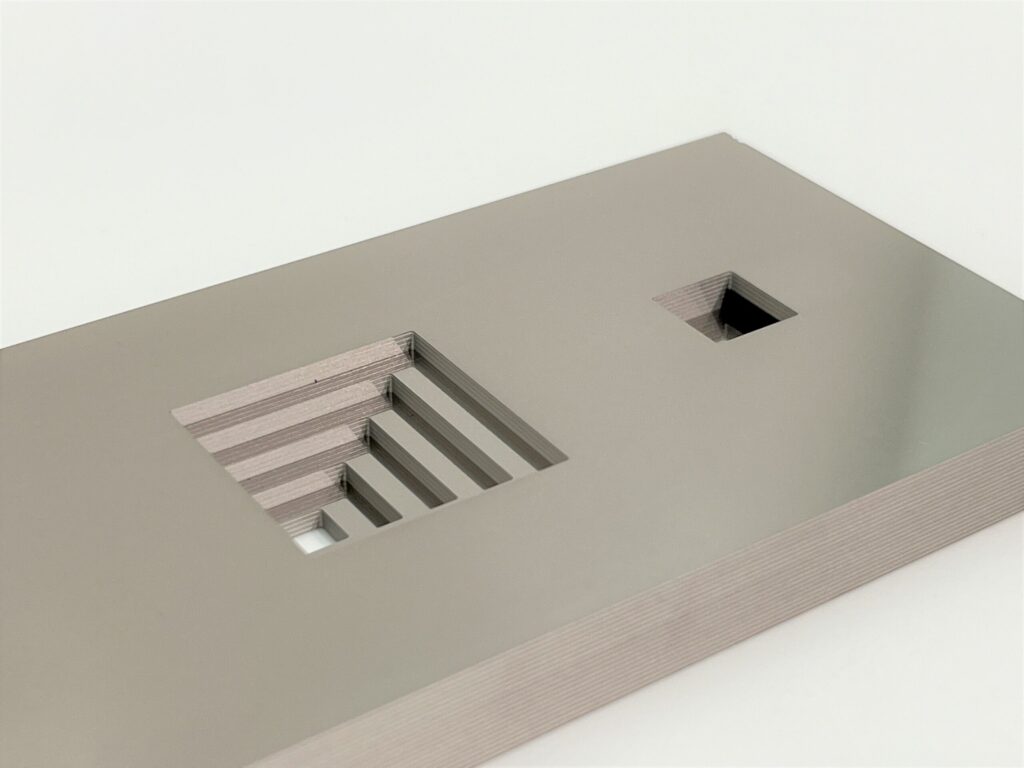
Use-Cases of Backing plate
Backing plates are used in the electronics and semiconductor industries and dissipate the heat generated during semiconductor manufacturing. Those plates made of materials with excellent thermal conductivity enable temperature control during the process and improve product quality in cases such as examples below.
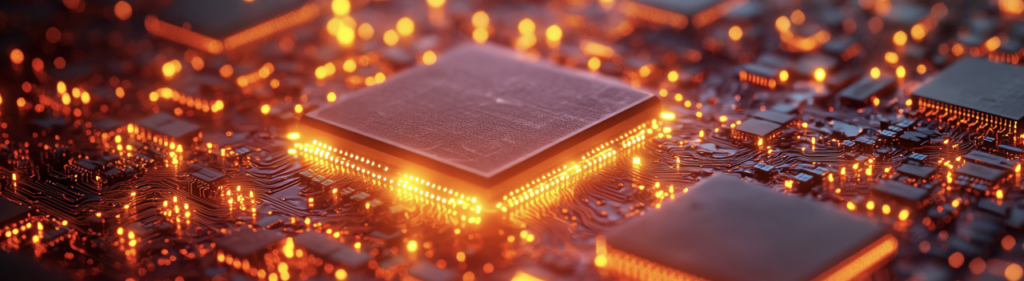
Sputtering Process
Used in sputtering equipment to efficiently heat and cool the target and substrate. They improve the deposition rate and uniformity of thin films and produces high-quality semiconductor devices.
Dry Etching Process
Used to efficiently cool a heated substrate during dry etching. They prevent substrate deformation and process defects caused by overheating and enable high-precision pattern formation.
CVD (chemical vapor deposition) process
Play an important role in maintaining uniform substrate surface temperature. They ensure uniform film thickness, adhesion, and material properties, and stabilize product quality.
Laser Processing Process
Localized heating occurs when irradiating substrates and components with lasers.
Backing plates prevente damage or shape changes to the part due to heat concentration, especially effective for parts that require precision processing.
Custom Backing Plates Design and Manufacture
UPT can help manufacture custom-designed backing plates.
Please consult with us if you are facing problems such as insufficient heat dissipation capacity with existing methods or lack of design flexibility to successfully incorporate them into your products.