Manufacturer 3D-Structured Metal Parts with
Diffusion Bonding and Photo Etching Technology
Diffusion bonding technology is one of bonding techniques that joints metals at atomic level by bringing their surface close together. This technique allows for creation of metal parts with complex 3D internal structures with high precision. Adhesives and spot welding are also used to bond metals commonly, but they have drawbacks such as peeling at high temperature, difficulty in cleaning, and creating gaps.
Diffusion bonding technology is a processing technology that allows fine and three-dimensional molding with high dimensional accuracy, and highly airtight bonding. Also, this technology is highly reliable, because it allows to maintain product performance and shape even after long-term use and in harsh environments such as high temperatures. UPT offers one-stop service for manufacturing metal parts by using diffusion bonding technology, from prototyping to mass production with short lead times.
Principle of Diffusion Bonding Technology (Mechanism)
Diffusion bonding technology is one of bonding techniques that joints metals at atomic level by applying heat and pressure. As a result, the metal atoms at the interface diffuse into each other, and strong bonding is formed. Diffusion bonding technology is suitable for joining metals with complex shapes and with dissimilar metals, and can withstand high temperatures and vacuum environments. It is widely used in advanced industries such as aerospace and electronics. Additionally, diffusion bonding technology is reliable because it generates little internal stress and defect in the joint.
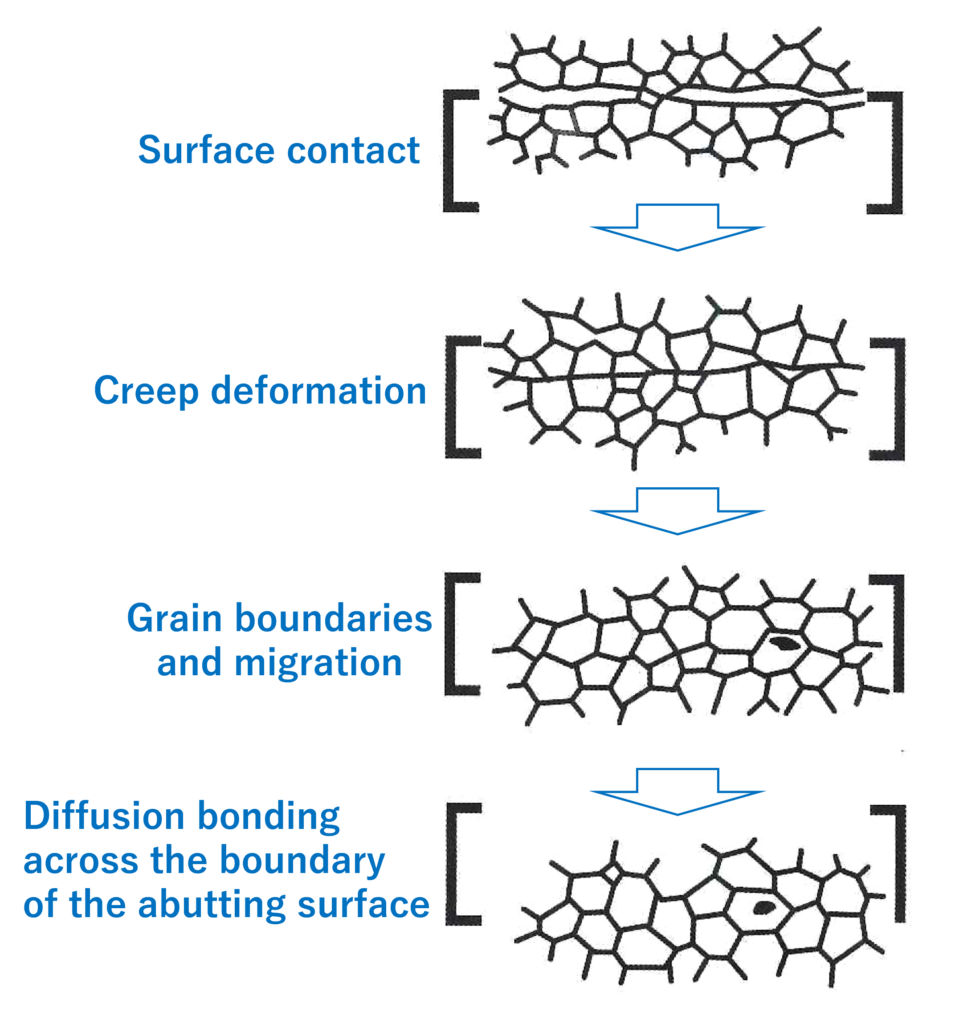
Benefits of Diffusion Bonding Technology
- High Reliability in harsh environments (such as high and low temperature)
- High fracture toughness and high temperature resistance
- Strong bonding strength
- Little post-bond alignment error
- Hermetic sealing
- High dimensional accuracy
- Little deformation
- No contamination
- Available to form 3D shapes and flow paths impossible with machining
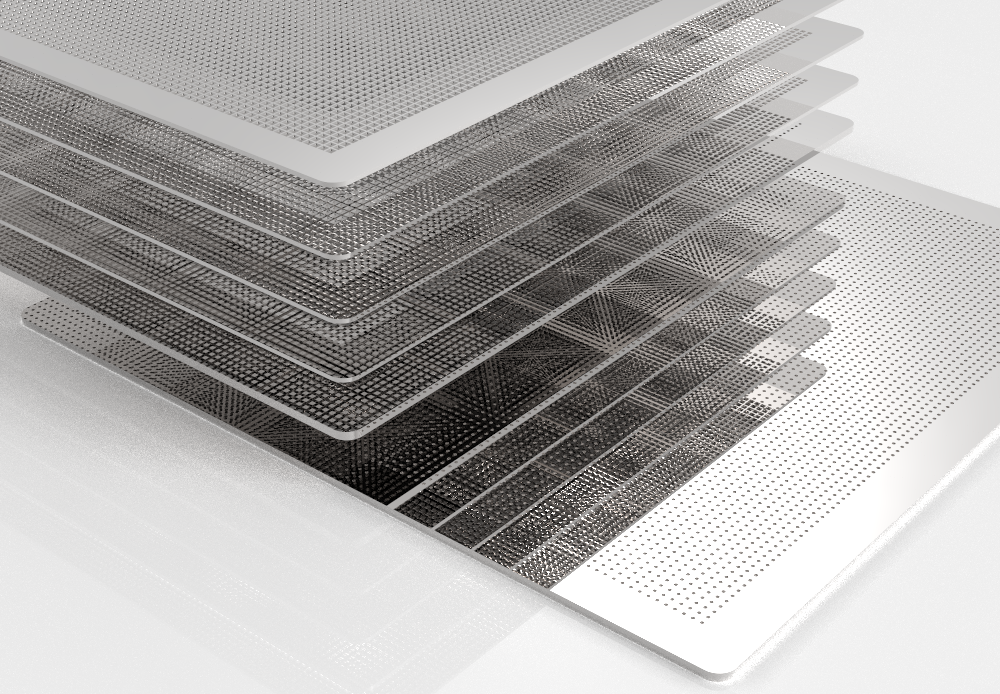
Diffusion Bonding + Photo Etching Technology
We have been creating new value such as following items by combining photo etching and diffusion bonding technology, and below are use-case examples.
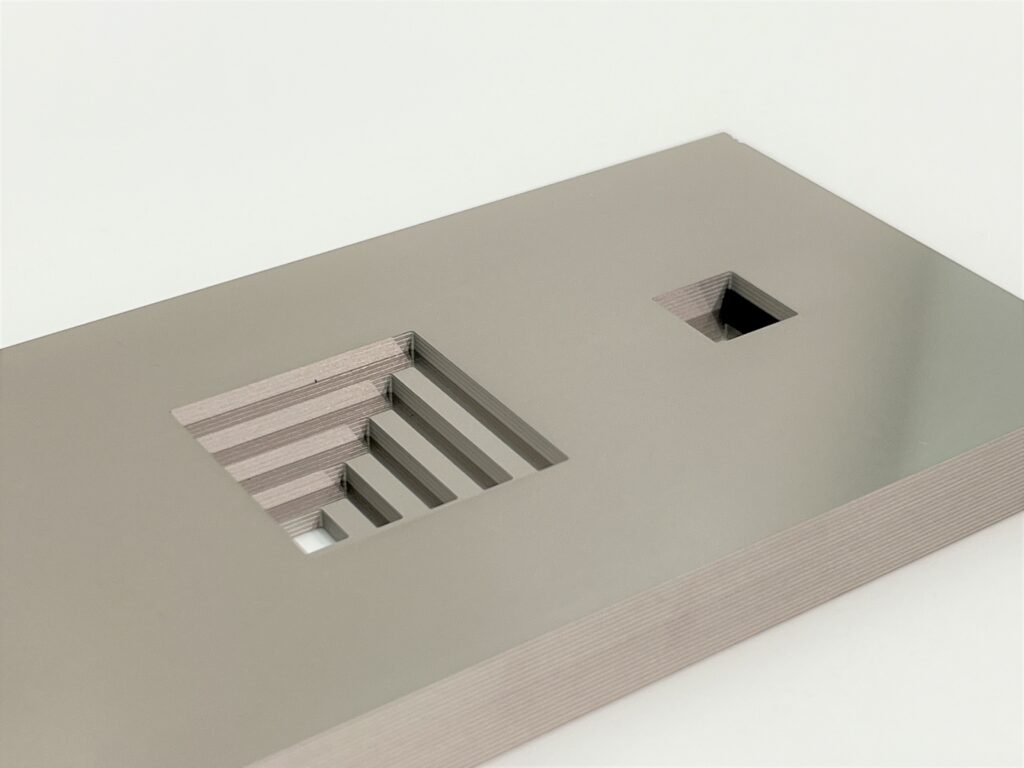
Plate thickness: 0.5mm × 10 layers
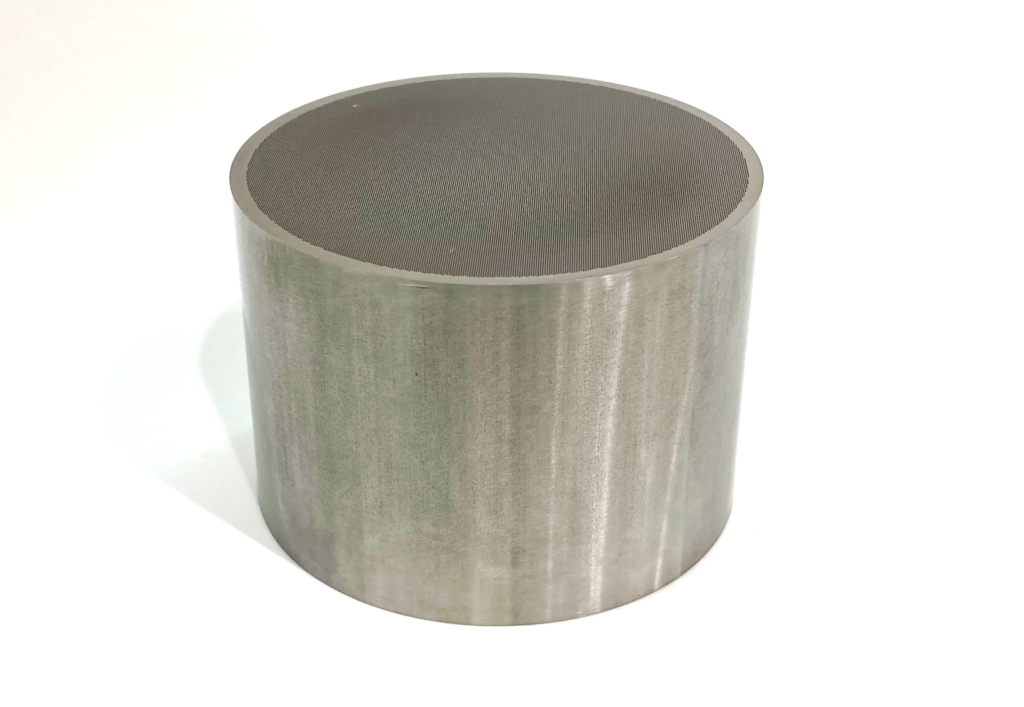
Plate thickness: 0.05mm × 1000 layers
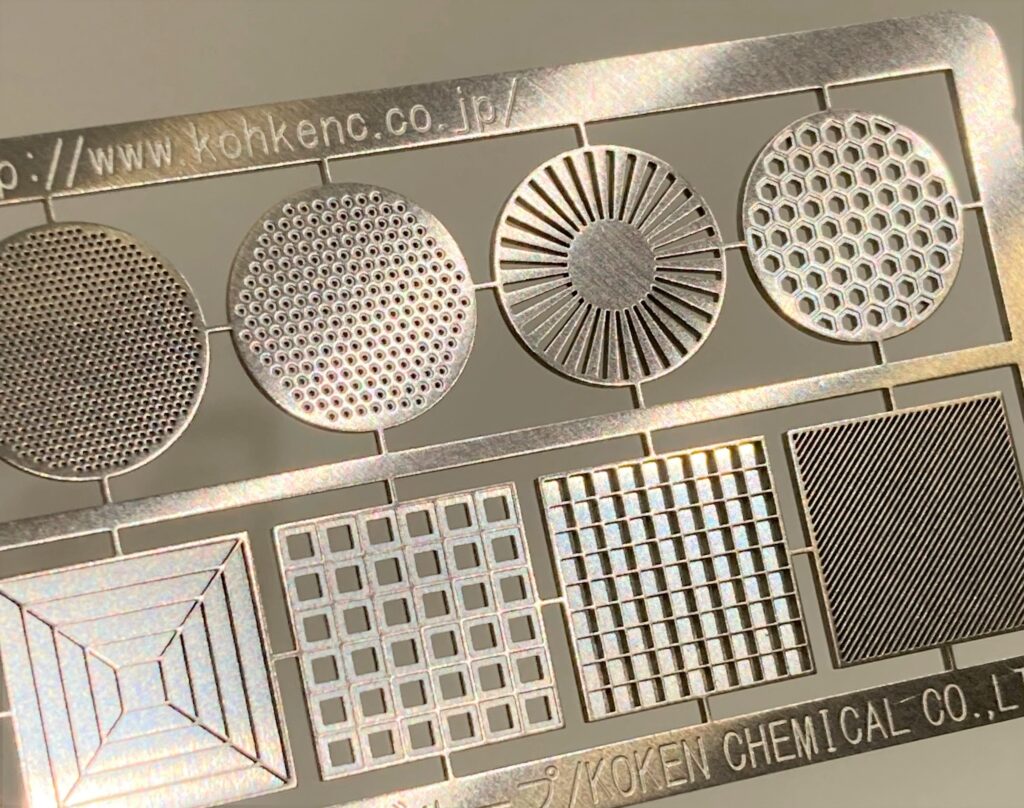
Plate thickness: 0.1mm × 7 layers
Benefits of Diffusion Bonding + Photo Etching Technology
- Capable of handling complex and intricate designs
- High Reliability in harsh environments (such as high and low temperature)
- High fracture toughness and high temperature resistance
- Little post-bond alignment error
- High dimensional accuracy
- Little deformation
- Available to form 3D shapes and flow paths impossible with machining
- Cost-effective from prototyping to mass production
Diffusion Bonding of Materials
Stainless Steel + Stainless Steel
SUS304、SUS430、SUS316、SUS631
Nickel/Nickel Alloy + Nickel/Nickel Alloy
Ni201、36Ni、42Ni、Permalloy
Aluminum + Aluminum
A5052、A6061、A6063
Iron + Iron
SPCC
Copper/Copper Alloy + Copper/Copper Alloy
C1020、C1100
Kovar + Kovar
KV-2、KV-6
Titanium + Titanium
TR270C
Stainless Steel + Copper
Contact us for more info about bonding dissimilar metals
Manufacturing and Processing Image
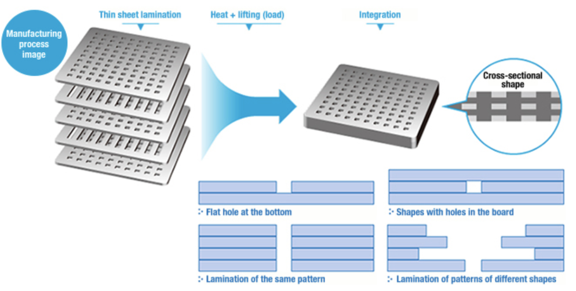
Cross Section of Diffusion Bonded Components
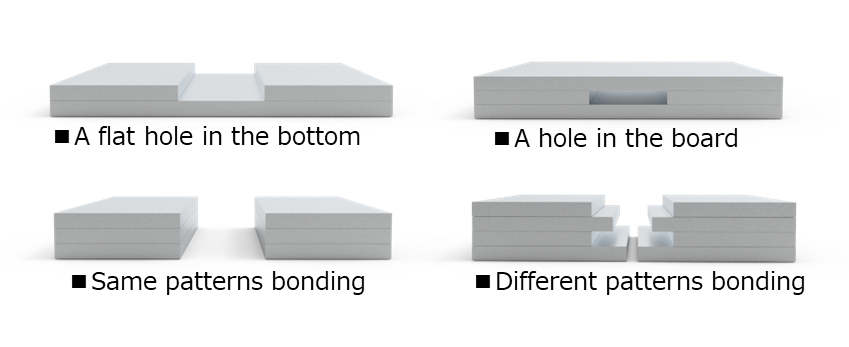
Examples of Diffusion Bonding + Photo Etching Technology
UPT offers a variety of products by combining diffusion bonding and photo etching technology. Here are some examples of our products portfolio.
Cooling Plates
Cooling plates are essential cooling components for heat management in electronic equipment and semiconductor devices. We can maximize the cooling performance of these devices by combining photo etching and diffusion bonding technology. We would like to offer thermal solutions tailored to your challenges.
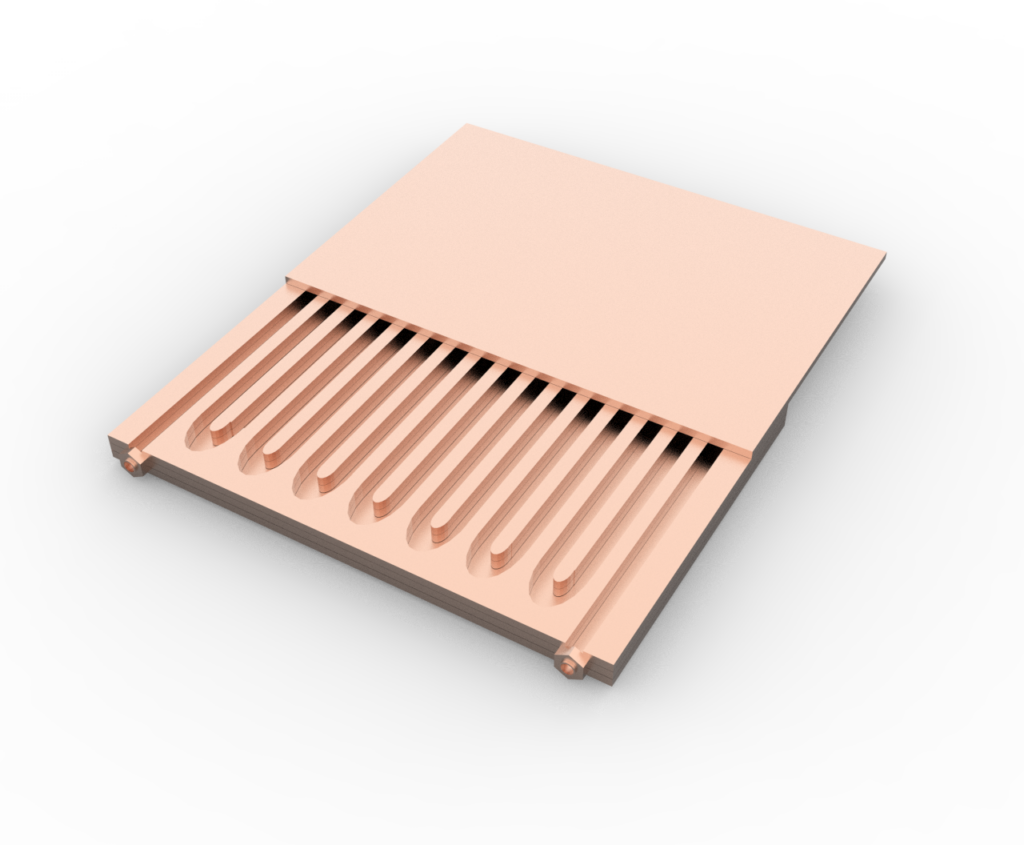
Fluid Control Bypass Mesh Filters
Thin mesh filters are integrated into precision instruments. We create high-aspect-ratio 3D mesh filters that prevent contamination. Our flat mesh filters resist dirt adhesion, have high strength, and can be used repeatedly over a long period of time. We can solve issues like misalignment during lamination (bonding), irregular hole diameters leading to unstable flow rate, pinholes, scratches, and gas burns.
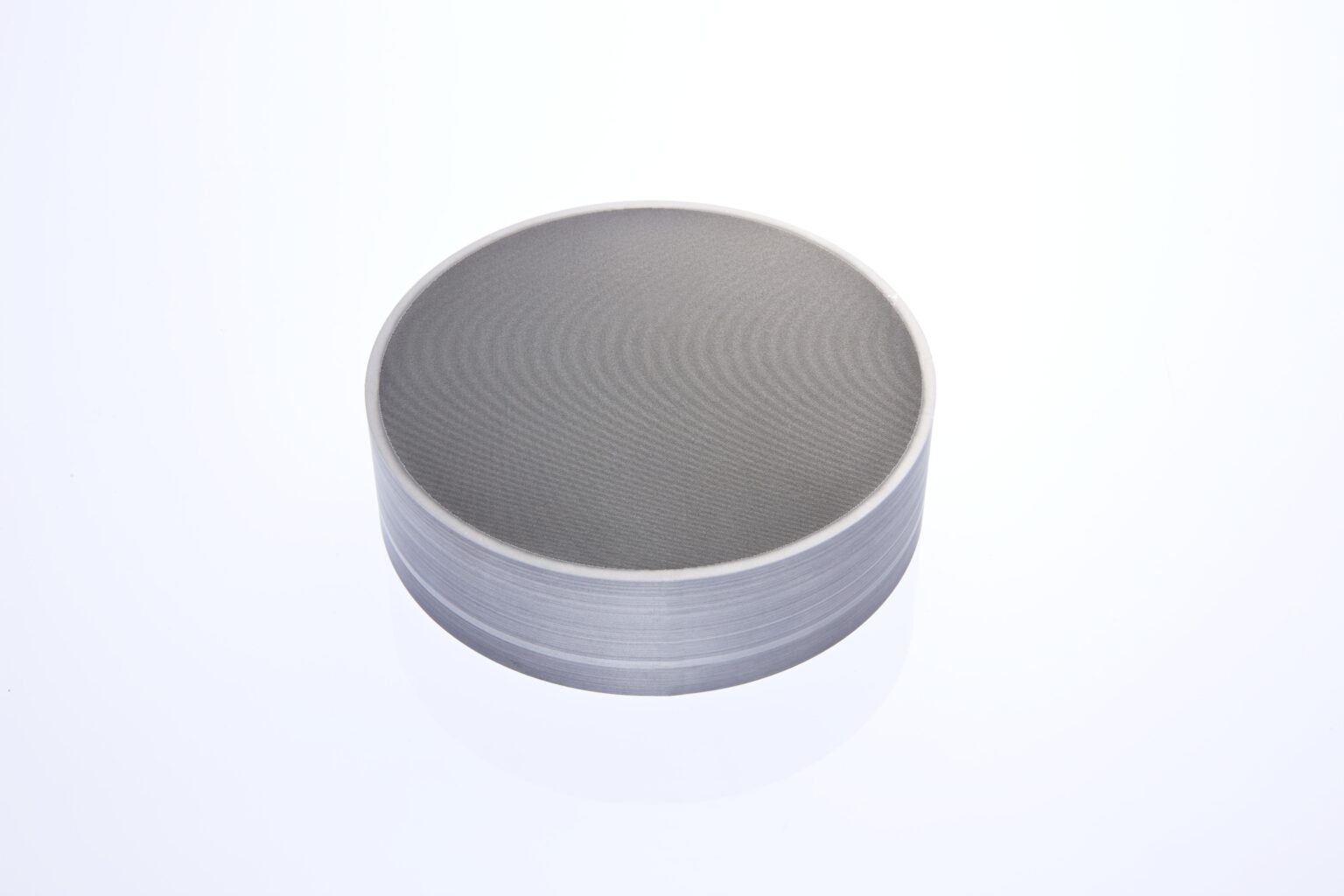
Transport Trays for Electronic Components
Transport trays (jigs) are used for positioning and transporting electronic components. UPT offers precise trays and jigs by combining photo etching and diffusion bonding technology, not just allowing for stable and precise positioning of tiny electronic components, but improving production efficiency in terms of component handling and extraction. There is no adhesive layer, ensuring products with such precise thickness.
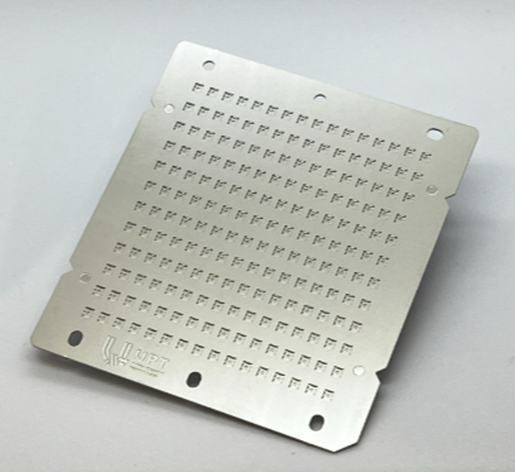
More Manufacturing Cases
- Heat Exchangers and Heat Sinks
- Lapping Carriers
- Inkjet Nozzles
- Filters
- Fuel Cell Separators
- Evaporation Masks
- Suction Plates
- Shim Assemblies
- Components for Electronic Equipment
- Precision parts trays and jigs
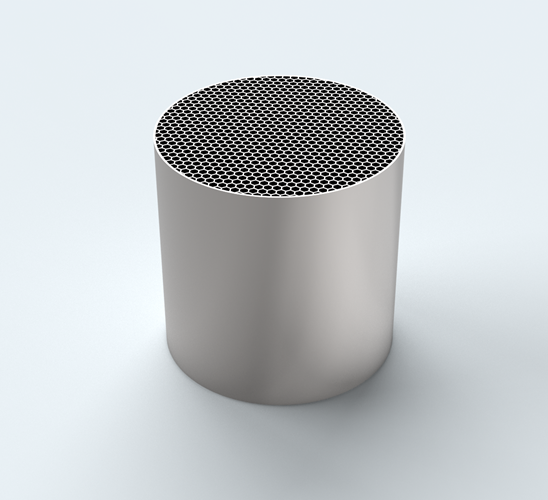